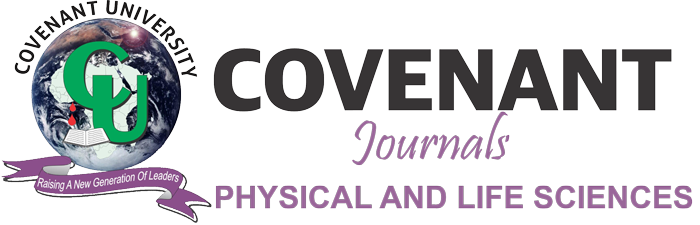
Several studies on design of Acceptance Life Test (ALT) focused on a subsystem (single system) totally ignoring its internal design. In most cases, it is not always possible to identify the components that cause the system failure or the cause can only be identified by a subset of its component resulting in a masked observation. This paper therefore investigates into the development of ramp-stress accelerated life testing for a high reliability parallel system that consist of two dependent components using masked failure data. This type of testing may be very useful in a twin-engine plane or jet. A ramp-stress results when stress applied on the system increases linearly with time. A parallel system with two dependent components is taken with dependency modeled by G umbel-Hougaard copula. The stress-life relationship is modeled using inverse power law and cumulative exposure model is assumed to model the effect of changing stress. The method of maximum likelihood is thereafter used for estimating design parameters. This optimal plan consists in finding the optimal stress rate using D-optimality criterion by minimizing the reciprocal of the determinant of Fisher information matrix. The projected plan is also explained using a real life example and sensitivity analysis carried out. This formulated model can help guide and assist engineers to obtain reliability estimates quickly with high reliability products that are sustainable.